If you’re in the manufacturing industry, you already know that data is critical to success. From tracking production processes to predicting consumer demand, data can reveal insights that help you optimize operations, improve product quality, and make informed decisions.
But with the rise of Industry 4.0 and the Internet of Things (IoT), data collection has exploded, leaving many manufacturers drowning in a sea of information. Unfortunately, collecting data is not enough – you need the right tools and techniques to turn it into valuable insights that drive growth.
Enter big data. Big data analyzes and leverages large, complex data sets to extract insights and improve decision-making. Big data can revolutionize the industry in manufacturing by providing real-time insights into production processes, supply chain management, and consumer behavior.
In this blog, we’ll explore the role of big data in manufacturing and discuss how you can turn your data into actionable insights. We’ll dive into the latest data management techniques, simplifying data analysis. So, whether you’re a small manufacturer or a global corporation, this blog will provide you with the knowledge and strategies you need to harness the power of big data and take your manufacturing operation to the next level.
Ready to turn your data into a competitive advantage and unlock the full potential of your manufacturing operation? Let’s get started!
Understanding Big Data in Manufacturing
As businesses adapt to the fast-paced world of technology, big data quickly becomes a critical component in the manufacturing industry. The sheer volume, variety, and velocity of data generated from production processes, supply chains, and customer feedback can no longer be ignored. Instead, it has become a primary driver of growth and success.
Manufacturing technology companies are at the forefront of leveraging big data in the industry. These companies provide hardware and software solutions that collect and analyze data from various sources, such as machines and sensors, to optimize production processes and increase efficiency.
Additionally, industry 4.0 consulting firms can provide valuable insights on integrating and optimizing new technologies to achieve maximum benefits.
Custom manufacturing software development is another area where big data can improve efficiency and productivity. Manufacturers can collect and analyze data in real time by creating software solutions tailored to a company’s specific needs, allowing them to make data-driven decisions that optimize production and reduce costs.
Manufacturing business software solutions can also be leveraged to collect and analyze data to drive growth and success. These solutions provide manufacturers with the tools to track inventory, manage production processes, and optimize the supply chain, resulting in increased efficiency and profitability.
Overall, big data transform the manufacturing industry, and companies that leverage it will gain a significant competitive advantage. By partnering with manufacturing technology companies, consulting firms, and custom software developers, manufacturers can optimize their processes and achieve new levels of efficiency and profitability.
Also, Read – From Automation to Digital Transformation: The Evolution of Industry 4.0
Types of Data in the Manufacturing Industry
Various data types can be collected and analyzed in manufacturing to improve business operations and decision-making. These include –

Production Data: This type of data provides information related to the manufacturing process, such as the number of products produced, cycle times, machine uptime and downtime, and other operational metrics. By analyzing production data, manufacturers can identify bottlenecks in their manufacturing processes and optimize production to reduce costs and improve efficiency.
Quality Data: Quality Data pertains to the level of excellence of products produced, including information on defect rates, scrap rates, and customer feedback. Scrutinizing this type of data enables manufacturers to identify areas for improvement and ensure that their products meet or exceed customer expectations.
Supply Chain Data: This type of data includes information related to the suppliers and vendors that manufacturers rely on to produce their products, such as lead times, inventory levels, and shipping times. Analyzing supply chain data can help manufacturers identify areas to reduce costs, improve delivery times, and ensure adequate inventory levels to meet demand.
Customer Data: Customer Data includes customer information, such as buying habits, preferences, and feedback. By analyzing customer data, manufacturers can gain insights into customer needs and preferences, which can help them customize their products and services to meet those needs.
In essence, by collecting and analyzing these different types of data, manufacturers can gain a deeper understanding of their business operations and make data-driven decisions to improve efficiency, productivity, and profitability.
Now that we know the data types, let’s move ahead and understand the best practices for collecting and analyzing this data.
Best Practices for Data Collection and Management in Manufacturing
Data collection and management are critical to ensure efficient operations, quality control, and continuous improvement. The following best practices can help manufacturers collect, store, and manage data effectively:

Develop a Data Collection Plan: To collect data in a structured and organized manner, it’s essential to develop a plan that outlines what data needs to be collected, how it will be collected, and when it will be collected. By following a plan, manufacturers can ensure that data is collected accurately and at the right time.
Use Automated Data Collection Systems: Automated systems such as sensors, Internet of Things (IoT) devices, and machine learning algorithms can help manufacturers collect real-time data without human intervention. As a result, minimizing the risk of errors and inconsistencies and enhancing efficiency in the data collection process.
Establish Data Quality Control Procedures: To ensure that the collected data is reliable and accurate, it is crucial to establish procedures for data quality control. These procedures can include data cleaning, validation, and normalization. By implementing such strategies, manufacturers can ensure that the data is consistent and trustworthy.
Implement Data Security Measures: Data security is paramount in any manufacturing environment. Manufacturers must implement various security measures to safeguard data from cyber threats, unauthorized access, and loss. This includes access controls, encryption, and regular backups. With robust security measures in place, manufacturers can maintain the confidentiality and integrity of their data.
Select Appropriate Data Storage Solutions: It is crucial to select appropriate data storage solutions like data lakes, cloud storage, or data warehouses capable of handling vast amounts of data, providing quick and easy access, and promoting seamless data sharing and collaboration.
Utilize Data Analytics Tools: Data analytics tools, such as business intelligence software, predictive analytics, and data visualization tools, can help transform data into actionable insights, facilitating data-driven decision-making and enhancing productivity, efficiency, and profitability.
Monitor and Evaluate Data Management Processes: It is crucial to regularly monitor and assess data management processes to identify areas for improvement, such as data quality, storage capacity, or analysis methods. Ensuring that data management practices are practical and efficient and that the organization utilizes the most effective techniques.
With that said, it’s clear that effective data collection and management are essential for achieving success in the manufacturing industry. Manufacturers can significantly improve data quality, efficiency, decision-making, and compliance by implementing best practices. In the next section, we’ll explore data analysis techniques to help turn that data into valuable insights and drive better business decisions. Stay tuned; we’ve got more exciting information ahead!
Data Analysis Techniques
Manufacturers collect large amounts of data. Still, the real value lies in the ability to analyze this data and extract insights that can drive decision-making as we know it.
Further, to better analyze the data, manufacturers can use the top techniques to analyze big data in manufacturing.

Descriptive Analytics: Descriptive Analytics is a technique that focuses on analyzing past data to identify trends, patterns, and relationships. This approach helps manufacturers better understand their past performance and identify areas for improvement.
Moreover, it can provide valuable insights into the root causes of issues and help manufacturers make informed decisions based on data.
Diagnostic Analytics: Diagnostic Analytics is a data analysis technique that helps manufacturers identify the relationship between different variables and the root cause of issues. It enables manufacturers to understand why certain events occur and how they can be prevented. By doing so, manufacturers can implement targeted improvements, leading to significant cost savings and process improvements.
Predictive Analytics: This technique uses statistical algorithms and machine learning models to predict future outcomes based on historical data. Predictive analytics can help manufacturers anticipate potential issues before they occur and take proactive measures to prevent them. It can also optimize production processes, improve product quality, and reduce downtime.
Prescriptive Analytics: Prescriptive analytics is a powerful data analysis technique that uses machine learning algorithms to recommend the best action based on historical and real-time data analysis. Manufacturers can optimize their production schedules, allocate resources more efficiently, and minimize waste by leveraging prescriptive analytics.
Moreover, this technique enables manufacturers to make data-driven decisions in real-time and address any issues as they arise quickly.
In essence, leveraging these data analysis techniques to extract valuable insights from big data can help improve efficiency, productivity, and profitability in a structured and systematic manner. However, choosing the appropriate data analysis technique is essential based on the specific business needs and goals.
However, It is important to note that while big data analysis can provide valuable insights and benefits, it also comes with challenges and limitations. What are these challenges? Let’s get to know!
Also, Read – Top 9 Data and Analytics Trends for 2023 and Beyond
Key Challenges and Limitations of Big Data in Manufacturing
Understanding the challenges and limitations of working with big data is critical to success in the manufacturing industry. Despite the potential benefits, various challenges and regulations are associated with working with big data in manufacturing.
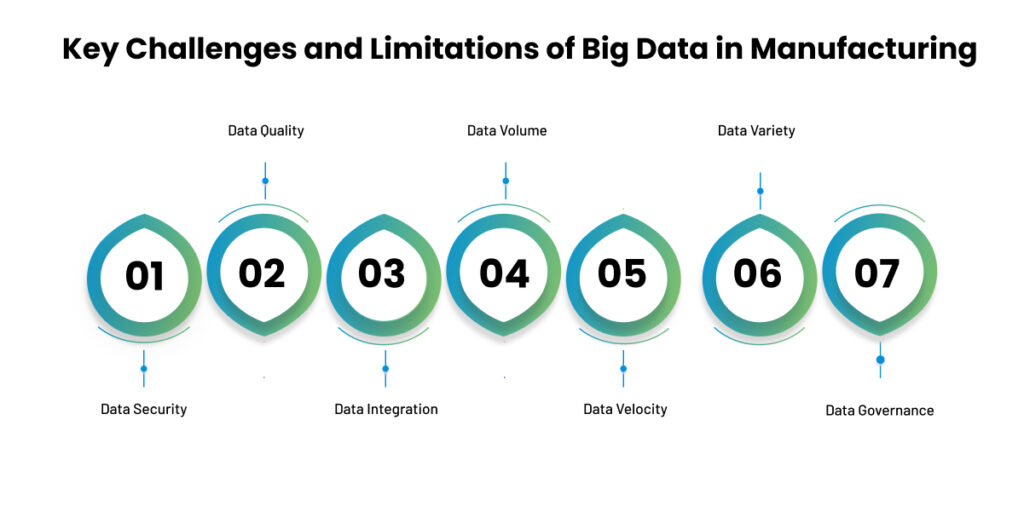
Data Security: Ensuring the security of sensitive data is a significant concern for manufacturers, as they handle large volumes of confidential information. Adequate security measures must be in place to safeguard data from breaches and cyber attacks.
Data Quality: Poor data quality can lead to inaccurate analyses and incorrect decision-making, making maintaining high data quality standards throughout the data collection and analysis process essential.
Data Integration: Integrating data from various sources can be challenging, as data can come from different formats, systems, and references. Data integration is necessary to provide a complete view of the manufacturing process.
Data Volume: Handling large volumes of data can be overwhelming, leading to slower processing times and increased storage costs. It is vital to have a scalable infrastructure to manage and process big data effectively.
Data Velocity: Data in the manufacturing industry can be generated and processed at high velocities, making it challenging to keep up with real-time analysis and decision-making.
Data Variety: Data in the manufacturing industry can come in various formats, including structured, semi-structured, and unstructured data. Managing and analyzing different types of data requires specialized tools and techniques.
Data Governance: Data governance refers to the policies, processes, and controls to ensure data is managed ethically, legally, and securely. It is vital to have proper data governance frameworks in place to mitigate risk and comply with regulations.
By understanding these challenges and limitations and implementing best practices to address them, manufacturers can effectively leverage big data to drive growth and success in the manufacturing industry.
Conclusion
In conclusion, the role of big data in manufacturing cannot be overstated. The manufacturing industry is rapidly evolving, and data-driven insights are becoming increasingly important for companies to remain competitive. With the implementation of best practices and data analysis techniques, manufacturers can unlock the full potential of their data and achieve success in the Industry 4.0 era.
Manufacturing technology companies and industry 4.0 consulting firms can play a critical role in helping manufacturers leverage big data effectively. By providing the latest tools and technologies, expert guidance, and customized solutions, these companies can help manufacturers overcome the challenges and limitations of working with big data.
However, it is essential to remember that working with big data has challenges and limitations. Manufacturers must be aware of these challenges and develop strategies to overcome them to realize the full benefits of big data. By doing so, they can improve efficiency, productivity, and profitability in a structured and systematic manner.
At the core, the manufacturing industry stands to gain a lot by harnessing the power of big data. It is time for manufacturers to embrace this transformative technology and use it to turn data into insights that drive growth and success.