The manufacturing industry is undergoing a massive shift with the advent of digital technologies. The traditional production methods are being replaced by innovative techniques that leverage cutting-edge technologies like artificial intelligence, the Internet of Things (IoT), and robotics. This shift towards digital transformation revolutionizes how manufacturers operate and deliver their products to the market.
Imagine a world where machines communicate with each other in real-time, optimize production processes, and identify potential inefficiencies. A world where quality control is automated and predictive maintenance is routine – the world of digital transformation in manufacturing.
Take, for example, the aerospace industry. By implementing digital twins, aerospace manufacturers can simulate the entire lifecycle of a product and identify potential problems before they occur. This allows for rapid prototyping and optimization of existing designs, resulting in significant cost savings and improved product quality.
Another example can be seen in the automobile industry, where companies are leveraging big data and analytics to optimize their supply chain and minimize waste. By tracking and analyzing data from various sources, manufacturers can make informed decisions that improve efficiency and reduce costs.
The benefits of digital transformation in manufacturing are clear, but the journey can be complex. Many challenges must be overcome, from investing in new technologies to developing the right talent. Contemplating the evolving manufacturing industry, we considered compiling a comprehensive guide to digital transformation in manufacturing, exploring the latest trends and best practices, and scrutinizing examples of companies leading the way.
So buckle up as we dive into the exciting world of digital transformation in manufacturing and discover how it’s shaping the future of production.
Understanding the “What” of Manufacturing Digital Transformation
The term “manufacturing digital transformation” has become increasingly prevalent in recent years, but what exactly does it mean? Simply put, digital transformation in manufacturing refers to integrating cutting-edge technologies and processes into the production line to drive efficiency, improve quality, and increase competitiveness.
At its core, manufacturing digital transformation revolves around adopting Industry 4.0 concepts, the Internet of Things (IoT), big data analytics, and other innovative technologies. These tools enable manufacturers to collect and analyze vast amounts of data, automate production processes, and ultimately make smarter, data-driven decisions.
By harnessing the power of these technologies, manufacturers can streamline operations, reduce waste and inefficiencies, and ultimately deliver a better product to their customers. Whether it’s through predictive maintenance to avoid unexpected downtime or the use of augmented reality for remote training and collaboration, digital transformation in manufacturing is all about using technology to drive results.
Now that we know what manufacturing digital transformation entails, it’s crucial to understand what drives the demand for manufacturing transformation. So, let’s dive deeper into these driving forces and see what’s fueling the digital transformation in manufacturing.
Also, Read – What is Digital Transformation? Here is Everything You Need to Know!
The Driving Forces of Manufacturing Digital Transformation
The demand for manufacturing digital transformation is driven by several key factors, each transforming the industry in its unique way. Here are the top drivers leading to the increased demand of digital transformation in manufacturing:
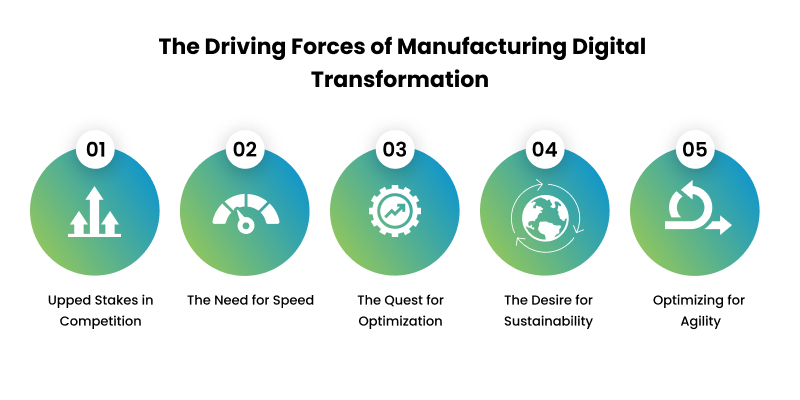
- Upped Stakes in Competition: The manufacturing sector has seen a surge in players, leading to cutthroat competition for market dominance. Companies leverage digital transformation to streamline operations and secure a solid competitive advantage in this race. The adoption of modern technologies has become necessary for manufacturers to stay ahead in the game and thrive amidst growing competition.
- The Need for Speed: In the fast-paced world of manufacturing, time is of the essence. Customers demand quick turnarounds and seamless delivery, and digital transformation equips manufacturers with the tools to meet these demands. By automating repetitive tasks, analyzing real-time data, and optimizing production schedules, manufacturers can speed up their operations and get products to market faster.
- The Quest for Optimization: The manufacturing industry has always placed a high value on efficiency, but digital transformation provides new and innovative ways to achieve it. With the help of technologies such as IoT and big data, manufacturers can gather and analyze vast amounts of data to pinpoint areas of their operations that can be optimized for improved performance.
- The Desire for Sustainability: As consumers and businesses become more environmentally conscious, the demand for sustainable manufacturing practices is rising. Digital transformation can help manufacturers reduce waste, lower their carbon footprint, and become more energy-efficient, meeting the growing demand for eco-friendly products and operations.
- Optimizing for Agility: The manufacturing industry is no longer a one-size-fits-all proposition. In the modern manufacturing era, the ability to quickly adapt to changing market conditions is more critical than ever. Digital transformation helps manufacturers streamline their processes and make their operations more agile, allowing them to pivot quickly in response to new customer demands or market trends.
Taken together, these factors make it clear that the demand for manufacturing digital transformation will only grow in the coming years. Further, if we look at the technical side, the next important step is to explore the key technologies fueling manufacturing digital transformation. Let’s get to it.
Also, Read – 5 Intelligent Automation Examples for your Organization
The Key Technologies fueling Manufacturing Digital Transformation
As we read above, the manufacturing world is undergoing a radical transformation driven by various cutting-edge technologies that are revolutionizing the way products are designed, manufactured, and delivered.

From Industry 4.0 to IoT and big data, the technologies empower manufacturers to optimize their operations, streamline their processes, gain a competitive edge, and change the game for manufacturers worldwide.
Industry 4.0: Also known as the Fourth Industrial Revolution, a key driver of manufacturing digital transformation – Industry 4.0 refers to the integration of advanced technologies such as IoT, artificial intelligence, and robotics into the manufacturing process, enabling manufacturers to improve their operations by analyzing vast amounts of data in real-time and making more informed decisions.
Resulting in a more agile, efficient, and responsive manufacturing process, which can increase productivity, reduce costs, eliminate bottlenecks, increase output, and enhance product quality.
IoT (Internet of Things): Another key technology critical in driving digital transformation in the manufacturing industry is non-other than IoT.
As IoT-enabled devices and sensors can collect and transmit real-time data from across the production line, these equip manufacturers with unprecedented levels of insight and control, helping them optimize their operations, reduce waste, improve product quality, and increase efficiency. In addition, IoT can help with predictive maintenance, enabling manufacturers to proactively address potential issues before they cause downtime or production disruptions.
Overall, IoT provides manufacturers with the tools they need to make data-driven decisions, drive innovation, and stay ahead in an increasingly competitive landscape.
Also, Read – Top 7 IoT Trends Driving Innovation Across Businesses In 2023
Big Data: The next transformative technology that is powering the digital revolution in manufacturing is Big Data. With the exponential growth of data generated by industrial processes, machines, and other sources, manufacturers are leveraging big data analytics to gain insights into their operations and make data-driven decisions.
By gathering, processing, and examining massive amounts of data, manufacturers can spot patterns, trends, and connections, resulting in enhanced efficiency, productivity, and quality. The significance of deriving value from big data is vital to staying ahead in the rapidly changing manufacturing landscape and realizing digital transformation’s full potential.
Artificial Intelligence: Artificial Intelligence is revolutionizing the manufacturing industry and transforming how things get done. By harnessing the power of AI, manufacturers can create smarter factories and automate tedious tasks, freeing up time for more value-added activities.
AI algorithms can analyze production data to identify inefficiencies and suggest improvements, helping manufacturers make data-driven decisions that boost productivity and drive innovation.
With the ability to constantly learn and adapt, AI is a powerful tool for manufacturers. By embracing AI, manufacturers can unlock new possibilities and shape the industry’s future.
Also, Read – How Artificial Intelligence is Shaping the World of Tomorrow?
Robotics: Next we come to Robotics. Integrating advanced robotics technology into the manufacturing process is creating a new era of efficiency, accuracy, and flexibility. From assembly line automation to complex tasks like material handling and quality inspection, robots are becoming indispensable tools for manufacturers that can help reduce lead times, increase productivity, and drive innovation, leading to a more competitive, sustainable, and efficient future for the industry.
Cloud Computing: With its ability to streamline operations and provide access to data-driven insights, Cloud Computing has emerged as a significant driving force behind the manufacturing industry’s digital transformation.
Whether small and medium-sized businesses or large enterprises, manufacturers of all sizes are leveraging the power of cloud solutions to enhance their competitiveness and position themselves for future growth.
By reducing the burden of managing IT infrastructure and freeing up resources for innovation, cloud computing empowers manufacturers to navigate the rapidly changing landscape of the modern manufacturing world.
Augmented Reality: Augmented Reality is revolutionizing the manufacturing industry, providing a new level of efficiency and effectiveness. By incorporating AR into their operations, manufacturers can enhance training, reduce errors, and provide a unique and immersive experience for their customers.
For instance, AR can be leveraged to guide technicians through complex assembly processes or provide real-time troubleshooting assistance, resulting in improved productivity and reduced downtime. Furthermore, by using AR in customer interactions, manufacturers can showcase their products in a new light and stand out in a crowded marketplace.
With AR, the possibilities are endless, and the impact on the manufacturing industry is significant. Adopting this innovative technology is just another example of how digital transformation drives growth and competitiveness in the manufacturing sector.
The Blueprint to a Successful Manufacturing Digital Transformation
By now, we have understood that the manufacturing transformation is driven by advancements in technology and the increasing demands of consumers. To stay competitive and meet the market’s changing needs, manufacturers must embrace digital transformation.
However, the journey toward digital transformation can be complex, and it’s essential to have a roadmap in place to ensure success.

Therefore, to help better understand, here are the critical steps involved in implementing a successful manufacturing digital transformation:
- Assess Current Systems: The first step towards digital transformation is to assess current systems and processes. This includes identifying inefficiency and areas where technology can be leveraged to improve operations.
- Select the Right Technology: With the rapid advancement of technology, many tools and solutions are available to manufacturers. Choosing the right technology that aligns with the company’s goals and can be integrated into the existing manufacturing process is essential.
- Integrating technology into the Existing Manufacturing Process: Once the right technology has been selected, the next step is integrating it into the existing manufacturing process. This involves mapping the technology solutions, defining the process flows, and ensuring seamless integration with the current systems.
- Continuously Evaluate and Optimize: Digital transformation is an ongoing process, and it’s important to continuously evaluate and optimize systems to ensure the technology is being used to its full potential.
By following these steps, manufacturers can successfully implement a digital transformation strategy and reap the benefits of improved efficiency, reduced costs, and increased competitiveness.
Wrapping it Up!
It’s no exaggeration to state that the world of manufacturing is undergoing a digital revolution, and companies that embrace this transformation will be the ones that thrive in the years to come. The utilization of digital technologies such as automation, AI, and IoT is revolutionizing the operations of manufacturers, bringing about unprecedented levels of efficiency, quality, and competitiveness.
From streamlining operations and reducing costs to improving quality and launching new products faster, the benefits of digital transformation are clear. And for companies that embrace these technologies, the growth potential is immense.
However, digital transformation encompasses more than just technology; it involves a shift in culture and perspective. Thus enterprises must be open to change, question established norms, and strive for ongoing progress. Only then can they unlock the full potential of digital transformation and secure their place in the future manufacturing landscape.
Ultimately, manufacturing digital transformation is not just a trend; it’s a necessity. To remain at the forefront and compete in a constantly changing market, leaders must embrace digital technologies and partner with a leading digital transformation consulting firm to fully realize the potential benefits.