As manufacturing becomes increasingly complex and competitive, the need for innovative solutions to optimize processes and improve product quality has never been greater. One such solution that has gained significant attention in recent years is the use of digital twins. A digital twin is a virtual replica of a physical object or system created using real-time data and advanced simulation software.
The concept of digital twins has been around for decades, but recent technological advances have made it more practical and cost-effective to implement in a manufacturing context. The potential benefits of digital twins in manufacturing include the ability to simulate various scenarios and optimize processes, improve communication and collaboration among different teams, and monitor production in real time.
In this blog, we will explore the role of digital twins in driving the future of manufacturing simulation and digitization. We will also discuss the benefits of using digital twins in manufacturing and their role in simulation and digitization. Moreover, we will examine some of the challenges and limitations of digital twins and emerging trends and technologies that will shape their future in manufacturing. So, sit tight and get ready to dive into the exciting world of digital twins in manufacturing!
Defining Digital Twins: Characteristics, Types, and Applications in Manufacturing
Digital twins are virtual replicas of physical objects or systems that are created using real-time data and advanced simulation software. They are used to simulate, monitor, and optimize the performance of physical objects and systems, including manufacturing equipment, production lines, and entire factories.
The significance of digital twins in the manufacturing industry lies in their ability to improve efficiency, reduce costs, and optimize product quality. You can use real-time data and predictive analytics to simulate different scenarios and optimize production processes. In this way, you can expect faster response times, which is essential for manufacturers seeking to stay competitive in a complex and rapidly evolving market.
Characteristics of Digital Twin in the Manufacturing Industry
Digital twins have become a game-changer in the manufacturing industry, providing a powerful tool for optimizing processes and improving product quality. These virtual replicas of physical objects or systems have several key characteristics that set them apart from traditional simulation models.
One of the primary characteristics of digital twins in manufacturing is their use of real-time data. It updates the virtual representation of the physical object or system and ensures accurate and up-to-date insights into its behavior and performance.
Another critical characteristic of digital twins is their interconnectivity. Digital twins are connected to the physical object or system they represent. It enables them to monitor and control their behavior and performance. This interconnectivity also allows digital twins to facilitate communication and collaboration between different teams, including designers, engineers, and operators.
Digital twins also use predictive analytics to forecast the behavior and performance of the physical object or system under different conditions. It analyzes data from sensors and other sources to predict potential issues and optimize processes to prevent them from occurring.
Finally, digital twins come in two main types:
- Product Digital Twins are digital replicas of individual products.
- Process Digital Twins are digital replicas of manufacturing processes, production lines, or entire factories.
Both types of digital twins have unique manufacturing applications and offer numerous benefits for optimizing performance and reducing costs.
Overall, the characteristics of digital twins in manufacturing make them a powerful tool for improving efficiency, reducing waste, and improving product quality. With the increasing availability and affordability of digital twin technology, we can expect their use to become even more widespread in the years to come.
Applications of Digital Twins in Manufacturing
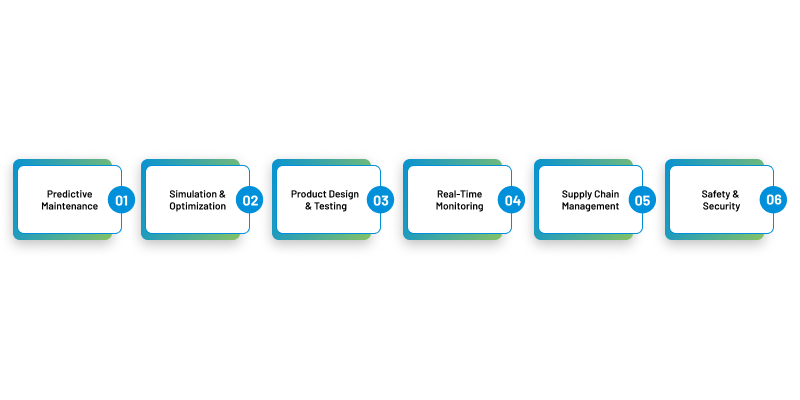
Digital twins’ applications in manufacturing are vast and varied. They offer numerous benefits for optimizing performance, reducing waste, and improving product quality. Let’s look at some of the most common applications of digital twins in manufacturing.
Predictive Maintenance
One of the most significant benefits of digital twins in manufacturing is their ability to predict when equipment or machines will fail. They analyze real-time data from sensors and other sources for early warnings of potential issues, so digital twins help in proactive maintenance.
Simulation and Optimization
Digital twins are used to simulate and optimize production processes. They can help to identify inefficiencies in the process, reduce waste, and improve efficiency. This, in turn, leads to increased productivity and reduced costs.
Product Design and Testing
Digital twins simulate and test product designs before they are physically built. This allows manufacturers to optimize the design and test its performance under different conditions. Digital twins help to reduce time to market and improve product quality.
Real-Time Monitoring
Digital twins are used to monitoring production in real time. They can provide valuable insights into the behavior and performance of equipment and systems. This, in turn, enables faster response times to issues and better decision-making.
Supply Chain Management
Digital twins can be used to optimize supply chain management. They can simulate the behavior and performance of the supply chain, identify potential bottlenecks, and optimize the flow of materials and products.
Safety and Security
Digital twins can enhance safety and security in the manufacturing process. By simulating and analyzing potential hazards, digital twins can help identify risks and take proactive measures to prevent accidents and ensure worker safety.
At their core, digital twins have revolutionized the manufacturing industry, providing manufacturers with powerful tools to optimize processes, reduce costs, and improve product quality. The characteristics of digital twins, including their use of real-time data, interconnectivity, and predictive analytics, make them a valuable asset for manufacturers looking to stay competitive in an ever-changing market.
Having discussed the wide range of applications of digital twins in the manufacturing industry, let’s now delve deeper into the role of digital twins in simulation.
So, simulation is a critical aspect of the manufacturing process, as it allows manufacturers to optimize operations, test new products, and reduce the risk of errors and downtime. In the next section, we will explore the role of digital twins in simulation.
The Key Roles of Digital Twins in Simulation and Digitization
As we read above, one of the main areas where digital twins are being used is simulation, where they can simulate different manufacturing scenarios, optimize processes, and test new products before being physically built.
Moreover, you can improve communication and collaboration among different teams with real-time monitoring of production processes. So, let’s quickly delve into the roles of digital twins in simulation and digitization in more detail.
Role of Digital Twins in Simulation:

Simulation of Manufacturing Scenarios: Digital twins enable the simulation of various manufacturing scenarios, which helps in identifying potential issues before they arise in the real world.
Optimization of Processes: Simulate different processes with digital twins to identify areas where processes can be optimized to improve efficiency and reduce costs.
Testing New Products: Digital twins can be used to test new products before they are physically built. This helps in identifying any potential issues and refining the product design before it goes into production.
Real-Time Monitoring: Digital twins enable real-time monitoring of production processes, allowing for immediate response to any issues that arise.
Predictive Maintenance: You can analyze data from digital twins to predict when maintenance will be required for different equipment, reducing downtime and maintenance costs.
Role of Digital Twins in Digitization
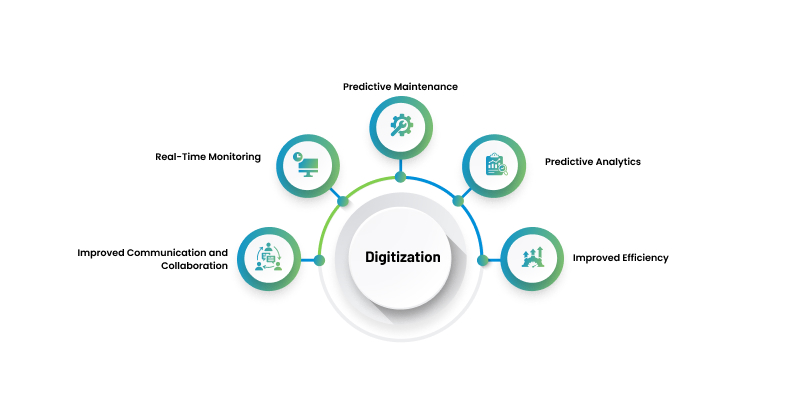
Improved Communication and Collaboration: Digital twins enable improved communication and collaboration among different teams by providing a common platform to share information and data.
Real-Time Monitoring: Digital twins enable real-time monitoring of production processes, allowing for immediate response to any issues that arise.
Predictive Maintenance: By analyzing data from digital twins, it is possible to predict when maintenance will be required for different equipment, reducing downtime and maintenance costs.
Predictive Analytics: Digital twins enable the use of predictive analytics to forecast future trends and identify potential issues before they arise.
Improved Efficiency: By digitizing processes, it is possible to improve efficiency and reduce costs. Digital twins enable the optimization of processes to improve efficiency even further.
In summary, digital twins play a crucial role in both simulation and digitization. In simulation, they enable the testing of different scenarios, the optimization of processes, and the testing of new products. In digitization, they enable improved communication and collaboration, real-time monitoring, predictive maintenance, predictive analytics, and improved efficiency.