As we find ourselves firmly rooted in the midst of 2023, it’s evident that the manufacturing world is undergoing a seismic shift driven by Industry 4.0 solutions. The digital revolution has ushered in an era of unprecedented connectivity and automation, transforming traditional production lines into intelligent, interconnected ecosystems. With the advent of smart manufacturing, factories are becoming more agile, efficient, and responsive than ever before, thanks to advanced manufacturing technology companies.
This blog will explore the cutting-edge trends shaping the smart manufacturing landscape for the remaining half of 2023 and beyond, focusing on integrating Industry 4.0 solutions. From advanced robotics and artificial intelligence to the Internet of Things (IoT) and the rise of additive manufacturing, we will dive into the fascinating developments propelling the industry forward.
So, continue reading as we uncover the transformative power of these emerging trends and their potential to revolutionize every aspect of manufacturing, in addition to the practical applications and real-world examples that illustrate their potential.
By the end of this blog, you will have gained valuable insights into the smart manufacturing trends for 2023-24 and be equipped with the knowledge to navigate this transformative landscape. Whether you are a manufacturing professional, an industry enthusiast, or simply curious about the future of production, this blog is your gateway to understanding the latest developments in smart manufacturing.
Now, let us dive headfirst into the world of smart manufacturing and witness the future unfold.
An Overview of Smart Manufacturing
Smart manufacturing, also known as intelligent manufacturing or Industry 4.0, represents a groundbreaking approach that empowers manufacturing technology companies to optimize production, streamline processes, and drive business transformation.
Leveraging emerging technologies and data-driven processes, Industry 4.0 has become the driving force behind a paradigm shift in the manufacturing industry. Traditional factories are now evolving into interconnected and intelligent systems that dynamically adapt to market demands, delivering unrivaled efficiency and performance.
Key Pillars of Industry 4.0 Solutions

Connectivity and Interoperability: Industry 4.0 solutions thrive on the seamless connectivity of devices, machines, and systems made possible by the Internet of Things (IoT) and advanced communication technologies. This networked ecosystem ensures smooth information exchange and interoperability, optimizing the manufacturing process.
Data Analytics and Artificial Intelligence: The core of smart manufacturing lies in harnessing and interpreting vast amounts of data. Through advanced analytics techniques, such as machine learning and artificial intelligence, business transformation consultants help manufacturers derive actionable insights. These insights lead to data-driven decision-making, predictive maintenance, and unparalleled operational efficiency.
Automation and Robotics: Industry 4.0 solutions are at the forefront of automating production processes, minimizing human intervention, and maximizing precision. With robotic systems and automated machinery integration, manufacturing technology companies can achieve higher productivity and consistent product quality.
Advanced Manufacturing Technologies: Industry 4.0 embraces the integration of cutting-edge technologies like additive manufacturing (3D printing), augmented reality (AR), virtual reality (VR), and digital twins. These innovations revolutionize product design, prototyping, and production processes, enabling faster iterations, customization, and optimized resource utilization.
Cybersecurity and Data Privacy: As smart manufacturing systems thrive on connectivity, ensuring robust cybersecurity and data privacy measures becomes paramount. Industry 4.0 solutions implement rigorous safeguards to protect intellectual property, sensitive data, and manufacturing systems from unauthorized access, ensuring a secure and resilient ecosystem.
Embracing Industry 4.0 solutions empowers manufacturing companies to unlock their full potential, transforming their operations into highly efficient, adaptive, and intelligent systems. By collaborating with business transformation consultants, they can leverage these key pillars to thrive in the future’s dynamic and competitive manufacturing landscape.
However, as the manufacturing industry continues to evolve, several emerging trends are set to shape the future of smart manufacturing. These trends are driven by the relentless innovation of manufacturing technology companies and their Industry 4.0 solutions.
Also, Read – How Industry 4.0 Technologies are Changing Manufacturing
Top Smart Manufacturing Trends 2023-24
Here are the top emerging trends in smart manufacturing that further enhance its impact on the industry. These trends drive efficiency, agility, and innovation, opening up new possibilities for manufacturers.
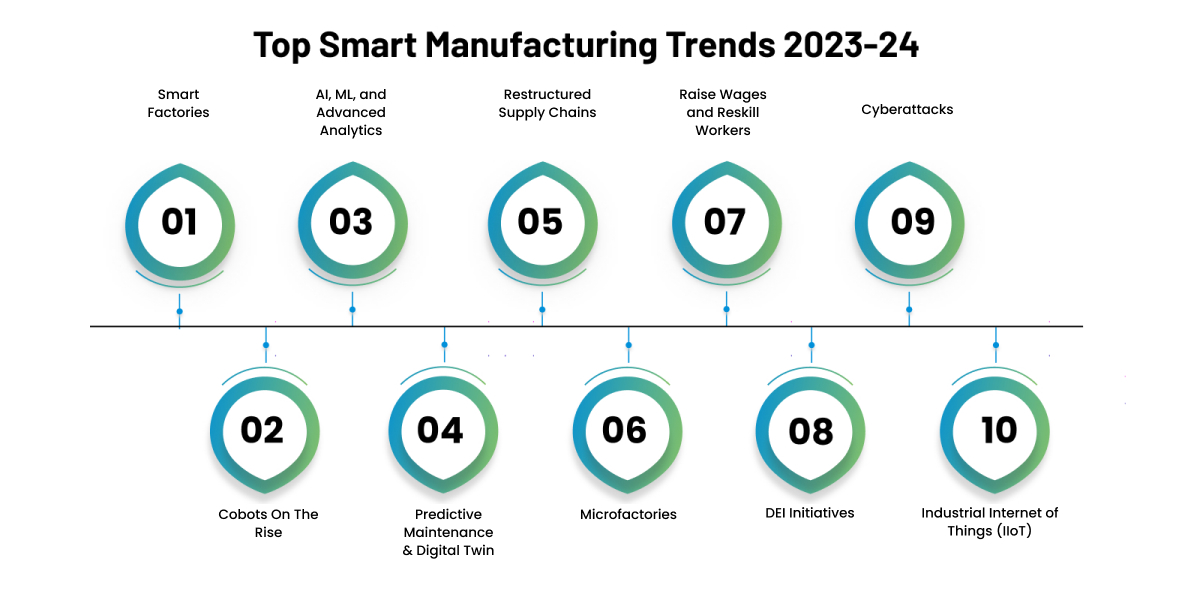
Smart Factories Are Changing How We Make Things
Smart factories, also known as Industry 4.0 or the Industrial Internet of Things (IoT), continue to revolutionize manufacturing processes. These factories integrate advanced technologies such as automation, robotics, sensors, and data analytics to optimize production, increase efficiency, and reduce costs. Connected machines and systems communicate, enabling real-time monitoring, predictive maintenance, and streamlined workflows.
Collaborative Robots (Cobots) Revolutionize Workforce
Cobots, equipped with intelligent technology and advanced safety features, are gaining momentum in the manufacturing industry. These versatile automation machines work harmoniously alongside human workers, taking on repetitive, hazardous, and less desirable tasks. By leveraging cobots, employees can redirect their efforts towards more valuable functions, optimizing productivity and efficiency in smart manufacturing environments.
Also, Read – The Growing Adoption of Collaborative Robots (cobots) in Manufacturing.
AI, Machine Learning, and Advanced Analytics Drive Efficiencies
Artificial intelligence, machine learning, and advanced analytics are increasingly adopted in smart manufacturing to optimize processes and drive efficiencies. These technologies analyze large volumes of data generated by interconnected devices, enabling manufacturers to make data-driven decisions, automate routine tasks, and improve overall operational efficiency. AI and machine learning algorithms help in demand forecasting, quality control, predictive maintenance, and supply chain optimization, ultimately leading to cost savings and improved productivity.
Predictive Maintenance and Digital Twin Technology Reduce Errors
Predictive maintenance, enabled by IoT sensors and AI algorithms, continues to gain prominence in smart manufacturing. Manufacturers can predict and prevent equipment failures by monitoring equipment in real-time and analyzing data patterns, reducing downtime and maintenance costs. Digital twin technology creates a virtual replica of physical assets and is crucial in predictive maintenance. It allows manufacturers to simulate and optimize processes, test scenarios, and identify potential issues before they occur in the real world.
Supply Chain Restructuring Is Changing Where Products Are Made
Supply chain disruptions caused by the pandemic, geopolitical factors, and changing customer preferences have led to a restructuring of global supply chains. Manufacturers are diversifying their sourcing strategies, focusing on nearshoring or reshoring production to reduce dependence on distant suppliers. This trend aims to mitigate risks, ensure faster response times, and maintain better control over quality and logistics. Advanced technologies like 3D printing and localized micro-factories also contribute to this shift.
Microfactories Emerge as Commerce Evolves
Microfactories, compact and localized manufacturing facilities, are gaining traction in response to changing consumer demands and market dynamics. These small-scale factories are flexible and modular and can be easily deployed closer to customers or in urban areas. They enable on-demand production, customization, and reduced lead times. Microfactories are particularly suited for niche markets, limited production runs, and personalized products. Micro-factories’ rise aligns with the growing trend of agile and localized manufacturing.
Manufacturers Raise Wages and Reskill Workers to Combat Labor Shortage
The manufacturing industry faces a shortage of skilled labor, prompting manufacturers to raise wages and invest in upskilling and reskilling initiatives. Companies offer competitive salaries, benefits, and training programs to attract and retain talent. Automation and robotics are also being deployed to augment human workers, allowing them to focus on more complex tasks and reducing the impact of the labor shortage on productivity.
DEI Initiatives Aim to Recruit Women and Minorities
Diversity, equity, and inclusion (DEI) initiatives are gaining momentum in the manufacturing sector. Companies recognize the value of diverse perspectives and are actively working to attract and retain women and minorities in traditionally male-dominated industries. Manufacturers are implementing inclusive hiring practices, providing equal opportunities for career growth, and fostering inclusive work cultures. Manufacturers aim to enhance innovation, creativity, and overall business performance by promoting diversity.
Cyberattacks Cause Downtime and Information Leaks
As manufacturing becomes more interconnected and reliant on digital technologies, the risk of cyberattacks increases. Cybercriminals target industrial control systems, supply chain networks, and sensitive data, leading to downtime, financial losses, and compromised intellectual property. Manufacturers prioritize cybersecurity measures, implement robust security protocols, conduct regular audits, and invest in employee training to mitigate these risks and protect their operations and assets.
IIoT is (Still) THE Big Thing
The Industrial Internet of Things (IIoT) continues to dominate smart manufacturing trends. The proliferation of connected devices, sensors, and data analytics platforms is transforming factories’ operations. IIoT enables real-time monitoring, remote diagnostics, predictive maintenance, and improved overall operational efficiency. Manufacturers leverage IIoT technologies to optimize production, reduce costs, and improve product quality. As the technology matures, we can expect further advancements and innovations in IIoT.
In essence, the landscape of smart manufacturing is evolving rapidly, driven by advanced technologies and changing market dynamics. Smart factories are revolutionizing how we make things, incorporating automation, AI, and IoT to optimize production processes and increase efficiency.
Predictable supply chains are becoming a priority, with manufacturers leveraging AI and advanced analytics for better visibility and risk management. Predictive maintenance and digital twin technology are reducing errors and minimizing downtime. Supply chain restructuring and the rise of micro-factories reshape where products are made. Manufacturers address labor shortages by raising wages and reskilling workers.
However, alongside these transformative trends, smart manufacturing also faces significant challenges. And what are these challenges? Let’s have a look.
Also, Read – Industry-Specific Challenges in Manufacturing: How to Overcome Them
Challenges of Smart Manufacturing
As we look ahead to the future of manufacturing, it is clear that smart manufacturing is set to revolutionize the industry in 2023 and beyond. The convergence of advanced technologies such as AI, IoT, and analytics drives unprecedented efficiency, productivity, and innovation. However, navigating the challenges of adopting smart manufacturing is crucial amidst the excitement and opportunities.
One of the foremost challenges is ensuring cybersecurity in an increasingly interconnected landscape. Manufacturers must prioritize robust security measures and stay vigilant against evolving threats to protect their operations and valuable data. Integration of legacy systems can also pose hurdles, but with careful planning, the transition can be made smoother, enabling seamless connectivity and interoperability.
Data management and analytics are vital for harnessing the full potential of smart manufacturing. Manufacturers can derive actionable insights and make informed decisions by investing in robust data storage and analytics tools and establishing sound governance practices. Bridging workforce skill gaps is another critical aspect. By investing in training and fostering a culture of continuous learning, manufacturers can empower their workforce to leverage smart technologies effectively.
Cost considerations should not deter manufacturers from embracing smart manufacturing. A strategic approach, cost-benefit analysis, and phased implementation can make it financially feasible while delivering tangible returns on investment. Moreover, collaborating with government programs and exploring partnerships can offer additional funding avenues.
In embracing smart manufacturing, manufacturers must not overlook the significance of diversity, equity, and inclusion. By promoting diversity in the workforce, they can tap into a broader range of perspectives and experiences, fostering innovation and driving better business outcomes.
Further, to navigate the complex and competitive manufacturing era, manufacturers must seek guidance and support from digital transformation consulting firms with proven expertise in Industry 4.0 solutions.
Seeking Manufacturing technology companies will assist businesses in their journey toward adopting cutting-edge technologies and optimizing their manufacturing processes. By partnering with experts, manufacturers can gain valuable insights, access industry best practices, and receive tailored solutions to address their specific challenges, enhance operational efficiency, reduce downtime, and improve product quality.
So, without contemplating more, contact a renowned digital transformation consulting firm that excels in helping manufacturers with Industry 4.0 solutions that reciprocate growth, value, and impact.